


Positive Molding Technology is an important factor in production of HARDEX® products. Positive molding results in a more uniform density in the production of the brake pad. It also allows using less resin content in formulation of the brake pad which can lead to improvement in the fading characteristic of the brake pad. The brake pads produced by positive molding process is proven to have much better stopping performance. High resin increases fading, which can increase stopping distances up to 50%.
All HARDEX® brake pads are manufactured using the same positive molding process utilized by Original Equipment suppliers. Positive molding uses extreme pressure to compress the friction material and bond it to the backing plate. This process assures consistent friction material density throughout the pad, resulting in even wear and performance characteristics throughout the life of the brake pad.
CHANGE BACKING PLATES
POSITIVE MOLDING TECHNOLOGY MAIN FEATURES:
-
Maintains constant friction consistency
-
Ensures better braking performance
-
Delivers longer service life
-
Requires less resin material
-
Resists heat fade
![]() STEEL WIRE-DRAWING | ![]() CASTING | ![]() STEEL MESH |
---|

PREMIUM CV BRAKE PADS
Hardex®


HARDEX® BRAKES SIMPLY OFFER A VERY SIMILAR PERFORMANCE TO OEM REPLACEMENT PADS.
SPECIFICALLY ENGINEERED TO MEET THE RIGOROUS DEMANDS
OF TODAY’S COMMERCIAL VEHICLE BRAKING SYSTEMS
Hardex® Commercial Vehicle (CV) brake pads provide the ultimate in quality, safety, and superior braking comfort. Our premium CV brake pads are made from original equipment (OE) quality raw materials, perfectly designed to meet the needs of every type of commercial vehicle, under all temperatures and conditions.


In addition to these features, Hardex® has introduced a Coating Layer to its brake pads. The objective of the OE STC is to improve performance and extend the lifespan of the brake pads. Traditionally, the OE STC comprises a ceramic-based substance administered to the brake pad surface during manufacturing.
This coating procedure heightens crucial friction performance metrics.
The OE STC diminishes noise and optimizes performance for both brake pads
and disc rotors.
OE STC MAIN FEATURES:
-
Reduced Noise: OE STC can help reduce noise generated during braking.
-
Improved Wear Resistance: The material in the coating can provide increased resistance to wear and abrasion.
-
Enhanced Heat Dissipation: The coating can help dissipate heat more efficiently.
-
Better Performance: OE STC can improve braking performance.

Hardex® BRAKES
YOUR CERTIFIED PARTNER ON THE ROAD


Emark ECE R90 by VCA:
Hardex® has obtained ECE R90 certification, which is required for all brake products to be used throughout the European Union and other countries that have adopted to ECE regulations.

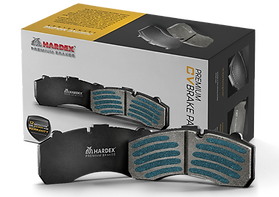

COMMERCIAL VEHICLE BRAKE PAD FEATURES:
-
Offers longer brake life and reduces disc wear
-
Provides superior braking in all temperatures and conditions
-
Features a minimum brake-in and bedding-in period
-
Optimizes the complete braking system.
-
Delivers ultra-quiet, smooth braking performance
-
Ensures optimal control and shorter stopping distances
-
Meets or exceeds OE standards
-
Uses 100% asbestos-free formulation



DESIGNED WITH CUTTING
EDGE TECHNOLOGY
Hardex® Commercial Vehicle brake pads are manufactured using the latest innovations and technology. From light commercial to heavy-duty and off-highway vehicles, our premium friction material formulation delivers outstanding durability and reduced wear that meets or exceeds OE manufacturer requirements. Manufactured with a host of the most up-to-date technology, you can count on Hardex® to provide your commercial vehicle with safe and effective braking every time.
PROTECT YOUR INVESTMENT
An out of commission vehicle can be a nightmare for many businesses. Fitting your vehicle with inferior brake pads can result in unnecessary downtime, costing you both time and money. Hardex® Commercial Vehicle brake pads will help protect your investment, keeping your vehicle where it belongs—on the road.